Revolutionizing Metal Casting with 3D Sand Printing Technology
Technology Overview
Sand casting 3D printing uses additive manufacturing to directly create sand molds for casting. By printing with a sand-like material and binder, this method allows for intricate molds without traditional tooling. Primarily used in foundries, 3D sand printing simplifies mold production, especially for metal parts. It increases efficiency by constructing complex shapes layer by layer and bonding sand particles. This technology has revolutionized casting, enabling faster, more flexible production of parts in various sizes and complexities.
Enhanced Design Flexibility
Cost Efficiency
Reduced Lead Times
Improved Accuracy
Our Machine
Select the Ideal 3D Printer Model for Your Unique Needs
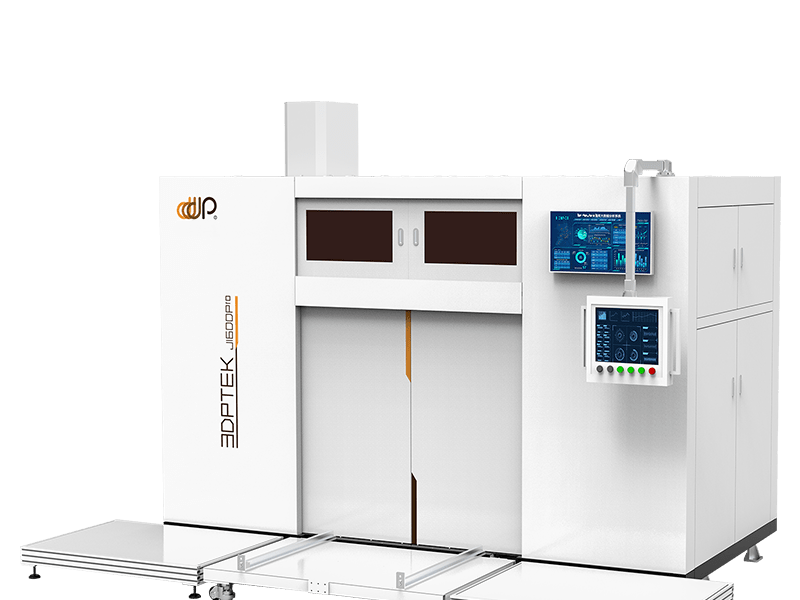
3DPTEK-J1600 Pro
The ultimate sand printing solution to bring unparalleled innovation to your business. Offering high reliability, it features premium core components for stable, dependable performance and minimal maintenance costs. Equipped with an internal nozzle circulation and automatic cleaning system, preventing clogging from adhesives. The orbital forming cylinder is automatically ejected at the push of a button, allowing part removal outside the machine for continuous, non-stop assembly line operation.
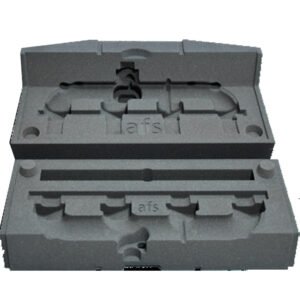

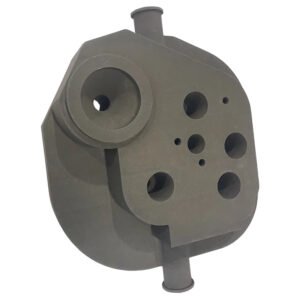

- Max. forming size: 1560×770×600mm
- Number of printheads: 6
- Forming thickness: 0.2-0.5mm
- Nozzle resolution: 400dpi
3DPTEK-J1600 Plus
This system is equipped with 6*1024 high-performance industrial printheads from top international brands, ensuring efficient and precise printing. It utilizes a servo motor, precision screw, and closed-loop control system to maintain accurate motion control. Additionally, the process includes logging and full quality tracking, ensuring continuous improvement in processing quality.
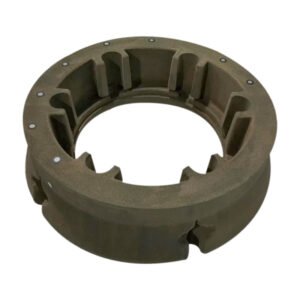
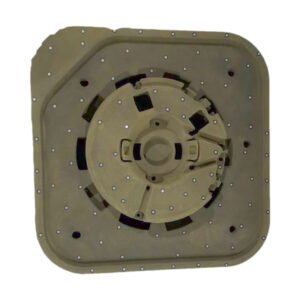


- Max. forming size: 1600×1000×700mm
- Number of printheads: 8
- Forming thickness: 0.1-0.5mm
- Nozzle resolution: 400dpi


3DPTEK-J1800
With the capability to handle large and heavy-duty molds, the 3DPTEK-J1800 can print sand molds weighing over 1.3 tonnes. This makes it ideal for producing large and complex castings, such as engine blocks and turbine housings. Designed to meet the demands of various industrial applications, it excels in manufacturing large-scale, intricate components.
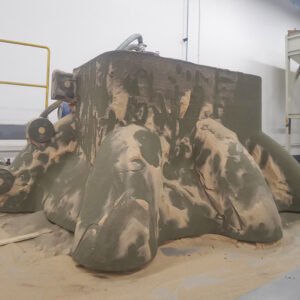


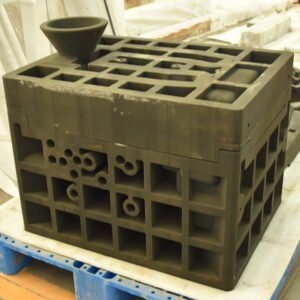
- Max. forming size: 1560×770×600mm
- Number of printheads: 6
- Forming thickness: 0.2-0.5mm
- Nozzle resolution: 400dpi
3DPTEK-J2500
The 3DPTEK-J2500 offers a wide range of material options, including quartz and ceramic sand, to accommodate various industries. It delivers excellent performance, with bonded products achieving tensile strengths of 1.5-2.5 MPa and low outgassing to reduce casting defects. Its integrated steel frame and precision-engineered components ensure long-term stability and reliability. The machine also features an intelligent German electrical control system for precise, safe operation, supported by robust, customizable software.
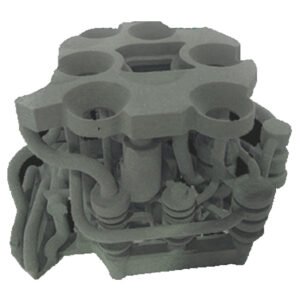

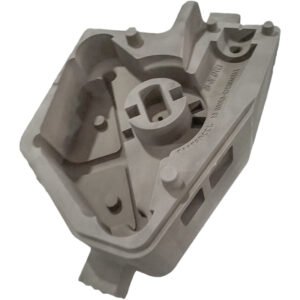

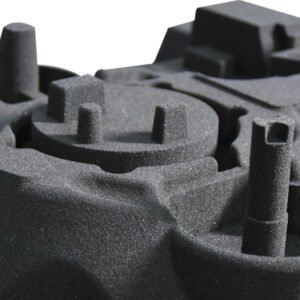
- Max. forming size: 1600×1000×700mm
- Number of printheads: 8
- Forming thickness: 0.1-0.5mm
- Nozzle resolution: 400dpi


3DPTEK-J4000
With the capability to handle large and heavy-duty molds, the 3DPTEK-J1800 can print sand molds weighing over 1.3 tonnes. This makes it ideal for producing large and complex castings, such as engine blocks and turbine housings. Designed to meet the demands of various industrial applications, it excels in manufacturing large-scale, intricate components.
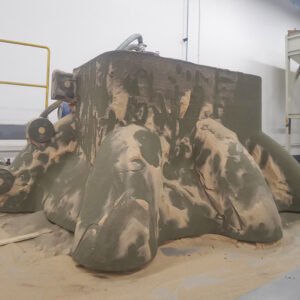


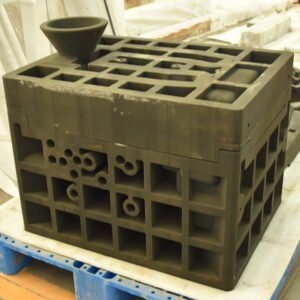
- Max. forming size: 1560×770×600mm
- Number of printheads: 6
- Forming thickness: 0.2-0.5mm
- Nozzle resolution: 400dpi
S1800
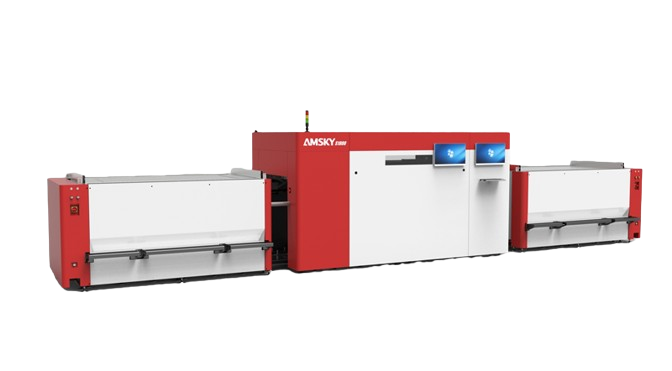
Tailored for small and medium-sized foundries
- Building Volume: 1800 × 1000 × 730mm
- Main machine dimensions: 9000 × 1900 × 1950mm
T1800
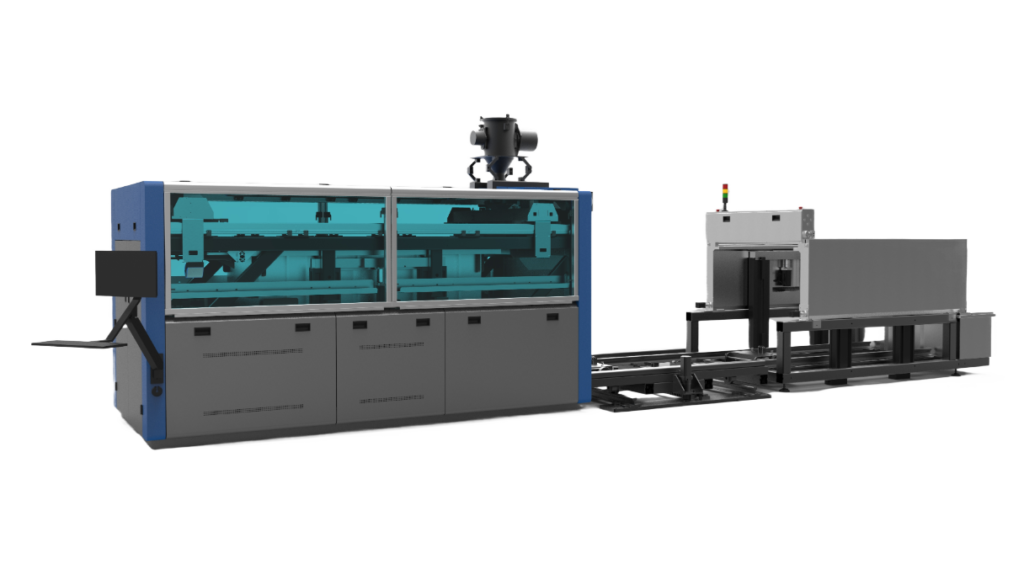
System solution for large-scale production of 3D sand Multi-machine linage mode
- Building Volume: 1800 × 1000 × 750mm
- Main machine dimensions: 3625×1768×2532
Contact us now to get to know more details about our machine!
Why Choose Our Machine?
Versatile Printing Capabilities
Large printing size, accommodating various sand casting mold needs.
Patented Technology
Equipped with a proprietary 3D printing head
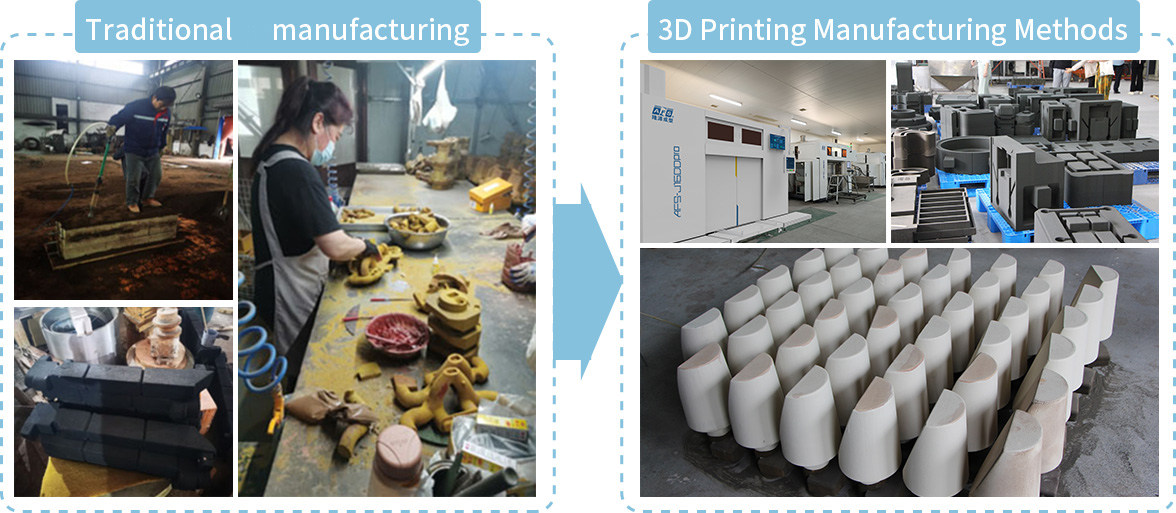
Compact and User-Friendly
Small footprint for easy installation and maintenance
Advanced Software Integration
Self-developed slicing and control software for efficient, automated slicing and printing
Case Presentation
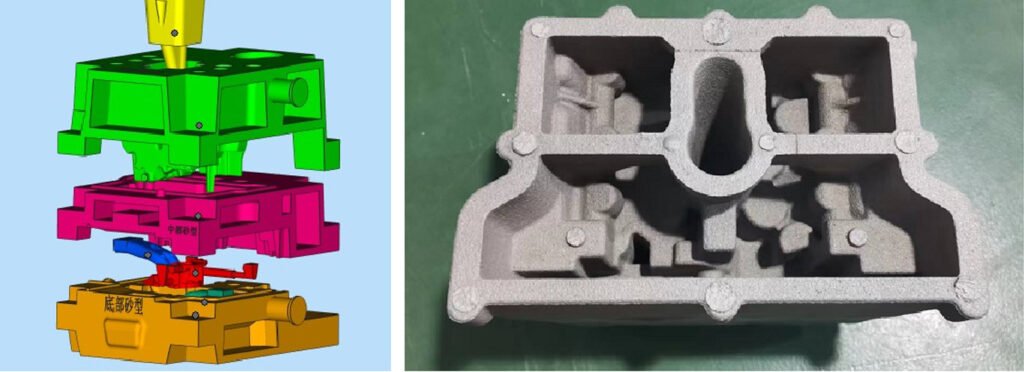

Automobile
This is a cylinder head for a Chery automobile. It passed tests for strength, air volume, dimensional accuracy, and surface quality, meeting customer specifications. The castings’ surface roughness meets standards, with no defects like excess material, pores, cracks, or slag.
Mechanical Part
This mechanical bracket’s sand mold meets all customer requirements for strength, gas emission, dimensional accuracy, and surface quality. X-ray inspections revealed no defects. The 1-month production cycle saved significant time compared to the 5-month wooden mold process.

Military Automobile
This exhaust manifold for a military vehicle meets all customer requirements for strength, gas emission, dimensional accuracy, and surface quality. With surface roughness below Ra12.5, defects like pores, cracks, and burrs are well controlled. The product passed operational testing and was approved.