SLS: The Future of High-Precision 3D Printing
The benefit of SLS includes:
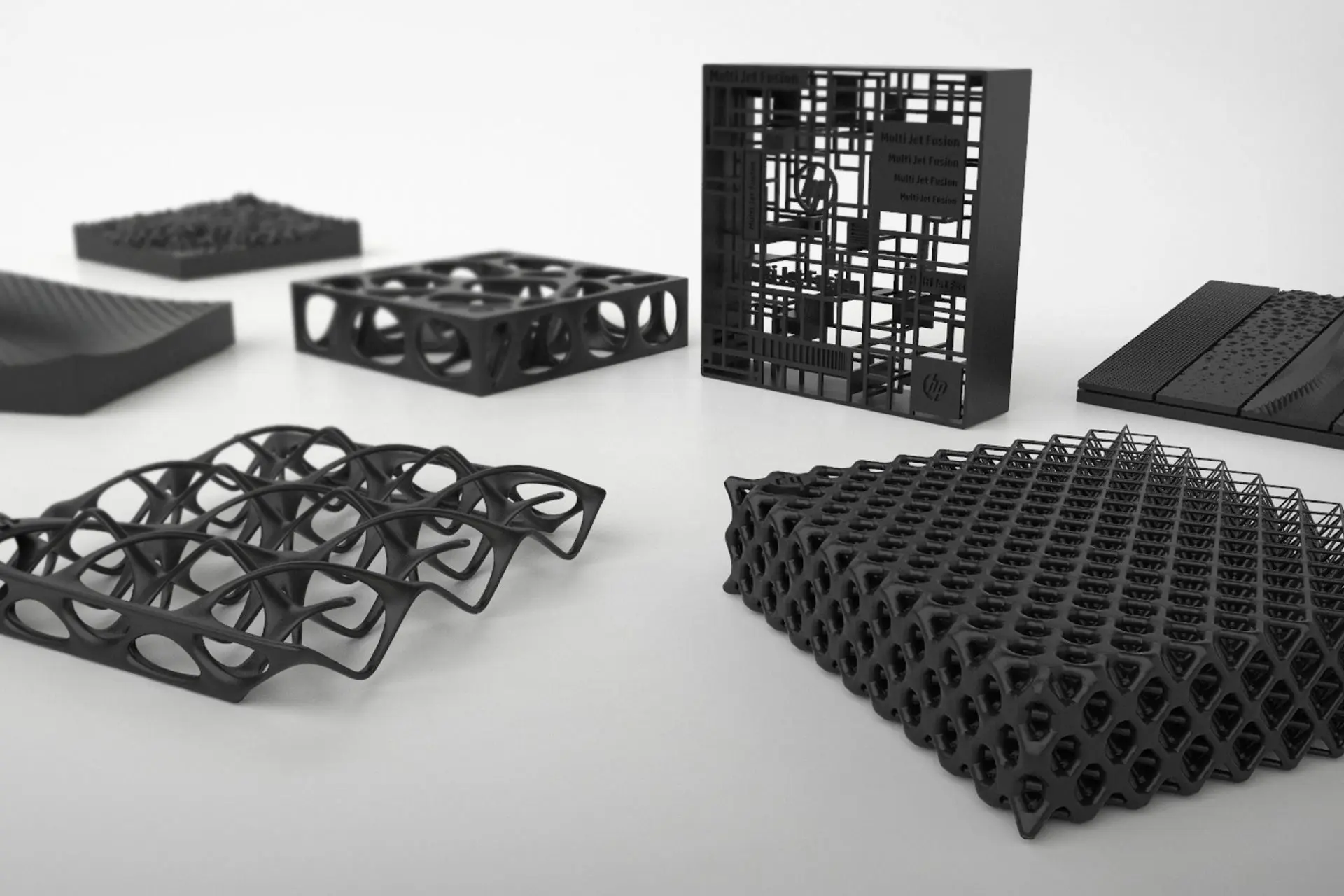
Sustainability: SLS produces less waste than other 3D printing technologies, as any unused powder can be recycled and reused in future prints.
Versatility: SLS can be used to create parts from a wide range of materials, including metals, plastics, and ceramics. This makes it a versatile technology that can be used in many different industries.
Complexity: SLS can produce complex geometries that would be difficult or impossible to create using traditional manufacturing methods. This is because the laser can sinter the powder in any shape, allowing for intricate designs and internal structures.
Speed: SLS is a relatively fast 3D printing technology, as it can produce multiple parts at once and does not require support structures like other technologies.
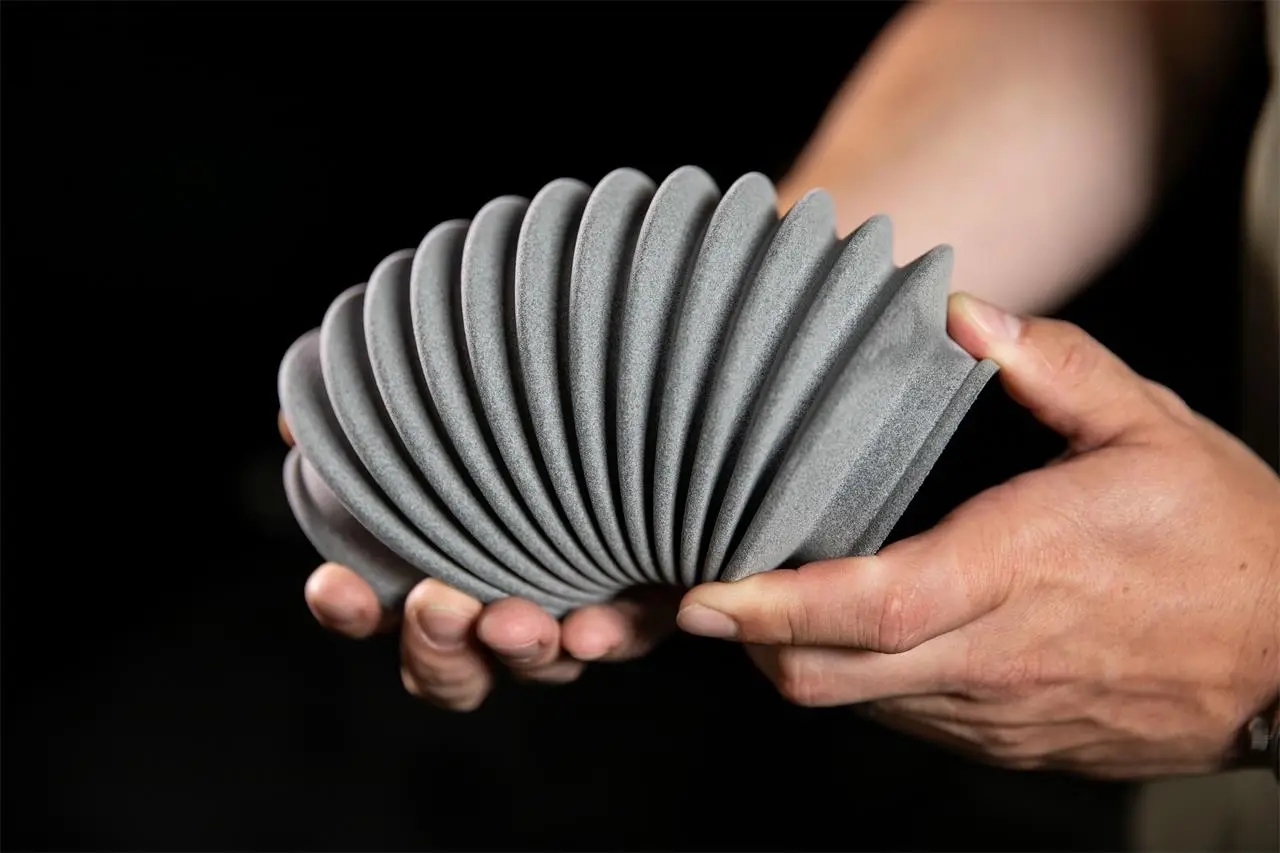
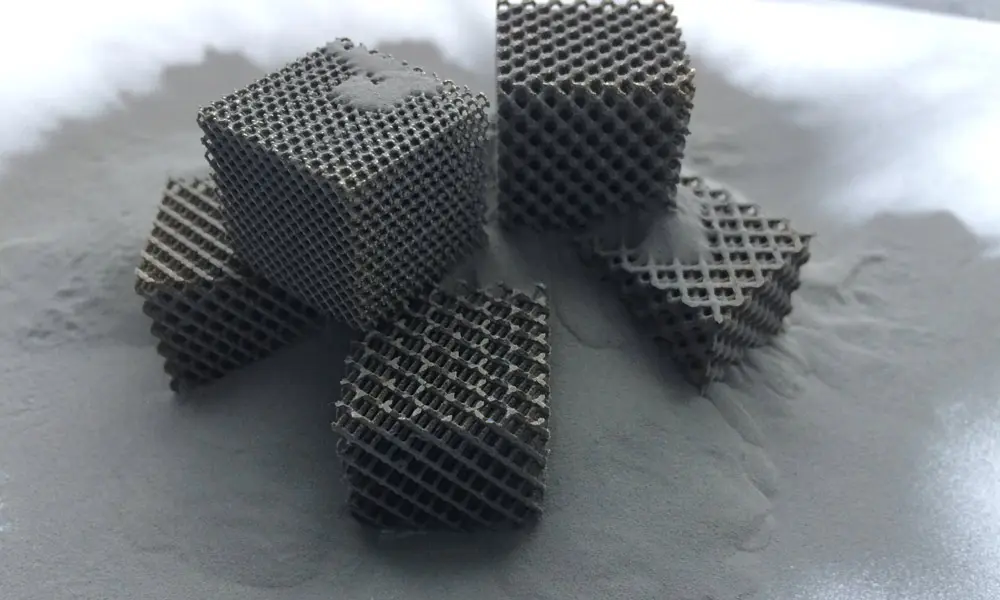
Cost-effectiveness: SLS can be a cost-effective way to produce small batches of parts, as it does not require expensive tooling like injection molding or casting.
Durability: SLS-printed parts are known for their high strength and durability, making them suitable for functional prototypes and end-use applications. The sintering process creates fully dense parts with excellent mechanical properties, capable of withstanding demanding conditions in various industries.
Contact Us now if you have any questions!
SLM: Crafting Strength with Laser Precision
The benefit of SLM includes:
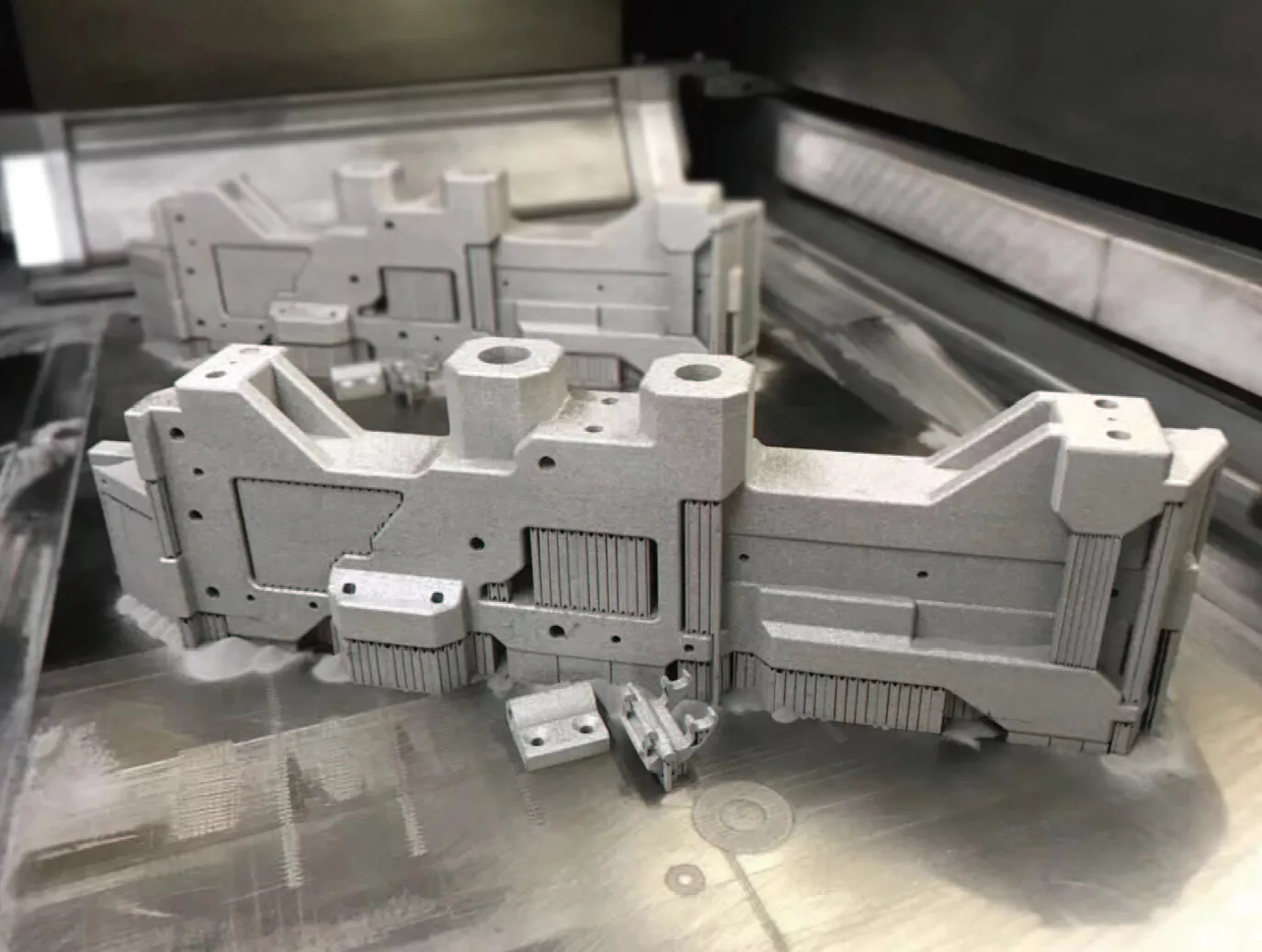
Material Versatility: SLM Metal can process a wide range of metals, including aluminum, titanium, and stainless steel, making it ideal for various applications across industries.
High Precision: Achieve intricate details and complex geometries with unparalleled accuracy, perfect for demanding engineering applications.
Enhanced Mechanical Properties: SLM Metal parts offer superior mechanical strength and durability, suitable for both prototypes and end-use products.
Reduced Lead Times: Rapid production capabilities allow for quicker turnarounds, reducing time to market and enabling faster innovation cycles.
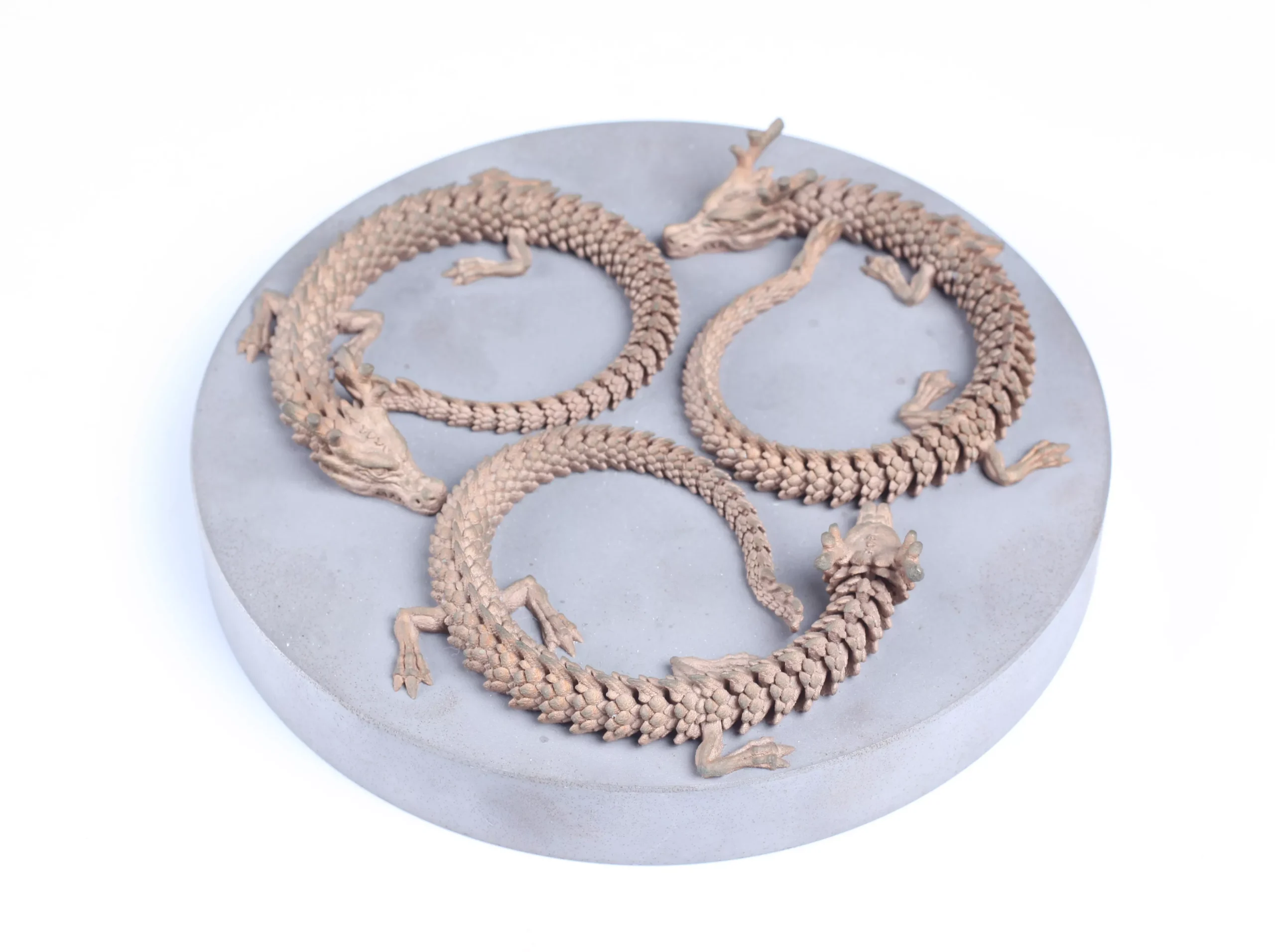
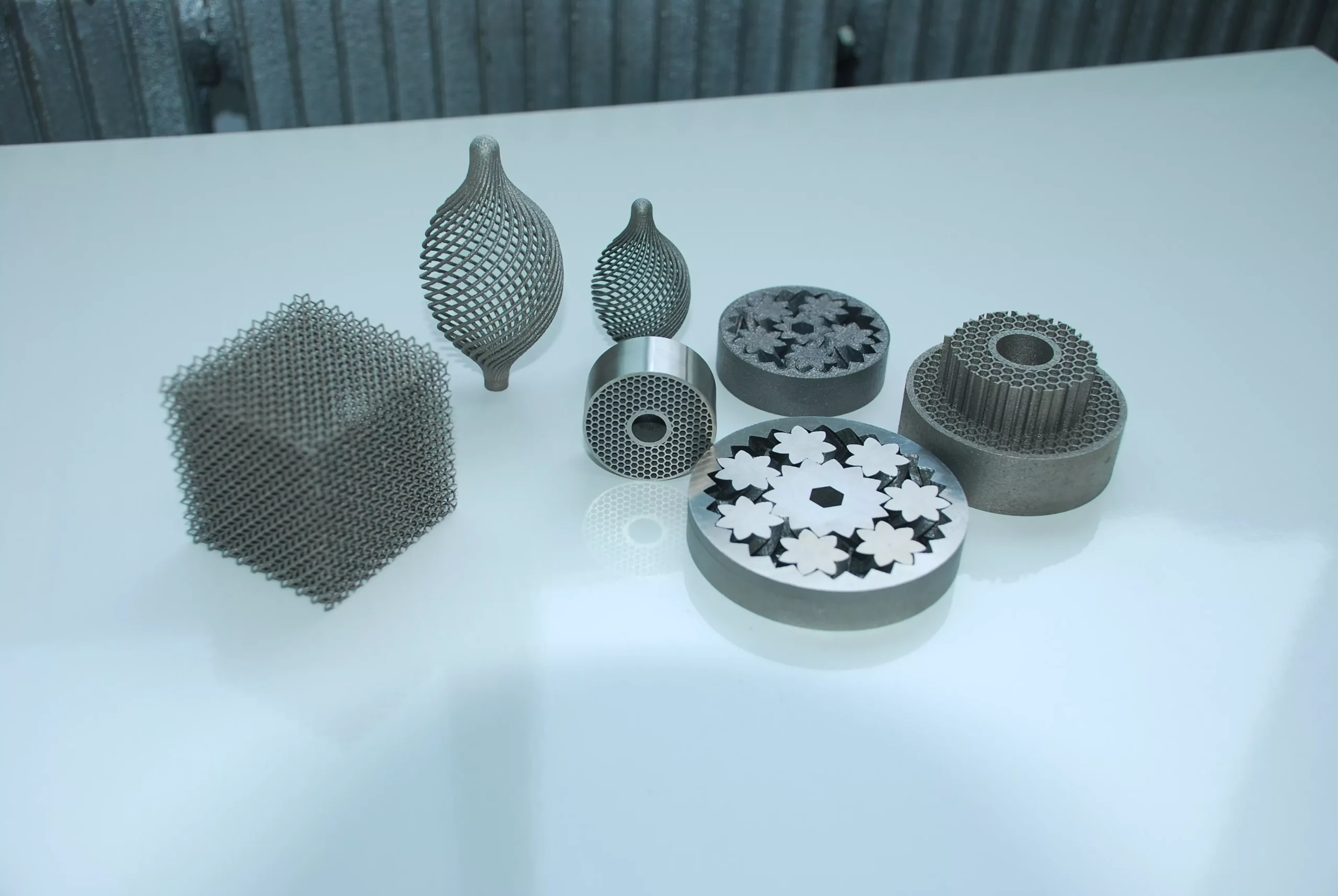
Lightweight Solutions: Optimize part design for weight reduction without compromising strength, ideal for aerospace, automotive, and other high-performance applications.
Customization and Design Freedom: SLM allows for unprecedented customization, enabling the creation of highly tailored and complex designs that are difficult or impossible to achieve with traditional manufacturing methods.
Contact Us now if you have any questions!
SLA/DLP: Achieve High-Resolution Brilliance with Resin Printing
SLA VS. DLP
Choosing the Right Technology
SLA (Stereolithography)
Uses a UV laser to cure resin layer by layer with high precision.
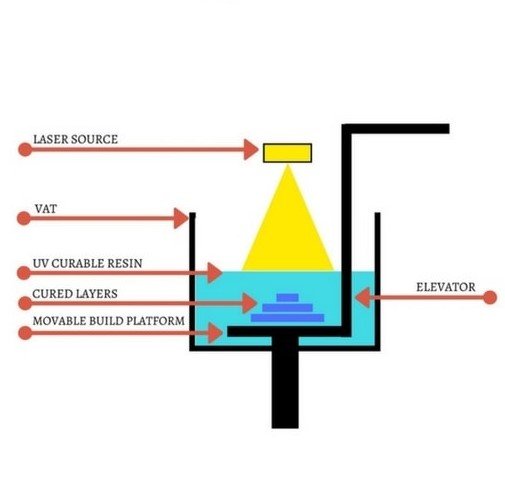
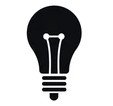
Slower due to curing one layer at a time.
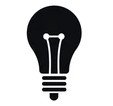
High resolution with excellent detail for complex parts.
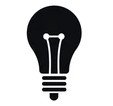
Produces very smooth surface finishes, minimal post-processing.
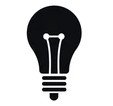
Broad range of resins including tough, flexible, and castable.
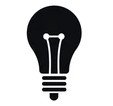
Typically more expensive due to laser precision.
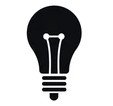
Ideal for intricate detail, smooth surfaces, and high accuracy.
DLP (Digital Light Processing)
Utilizes a digital projector to cure entire layers at once.
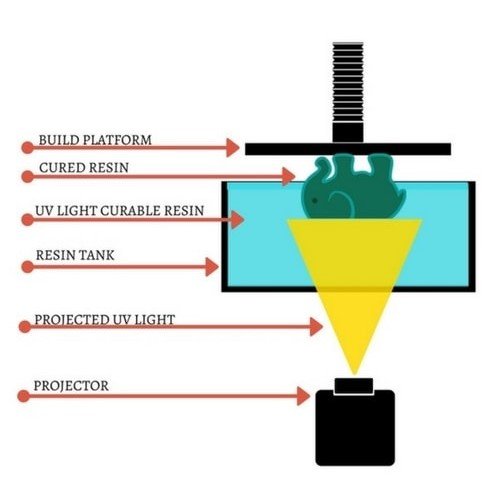
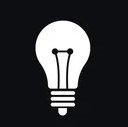
Faster as it cures entire layers simultaneously.
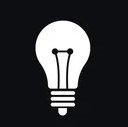
High resolution but detail may vary based on projector pixel size.
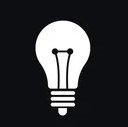
Smooth finishes, though slight pixelation may occur.
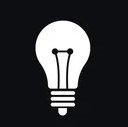
Supports various resins, but options may be slightly limited.
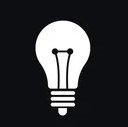
Often more cost-effective, especially for faster production.
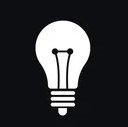
Best for faster production and balancing quality with speed.
The benefit of resin printing includes:
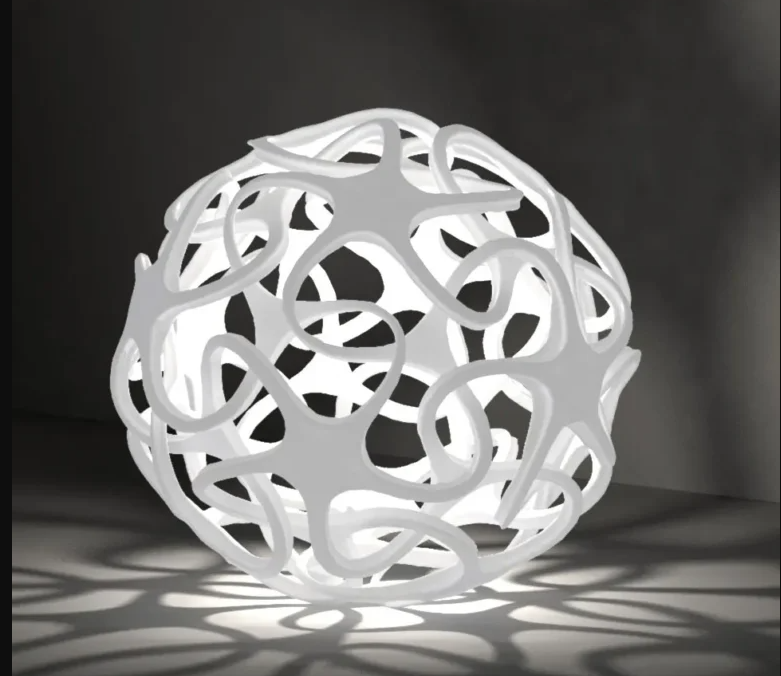
High Precision and Detail: Both SLA and DLP technologies deliver exceptional detail and accuracy, perfect for intricate designs and high-resolution prototypes.
Rapid Production: DLP offers faster printing speeds by curing entire layers at once, while SLA provides high precision for detailed, complex parts.
Versatile Material Options: A wide range of photopolymer resins is available, allowing for various properties such as flexibility, toughness, and high-temperature resistance.
Cost-Effective Prototyping: Both technologies enable cost-effective production of prototypes and small batches, reducing the need for expensive tooling and molds.
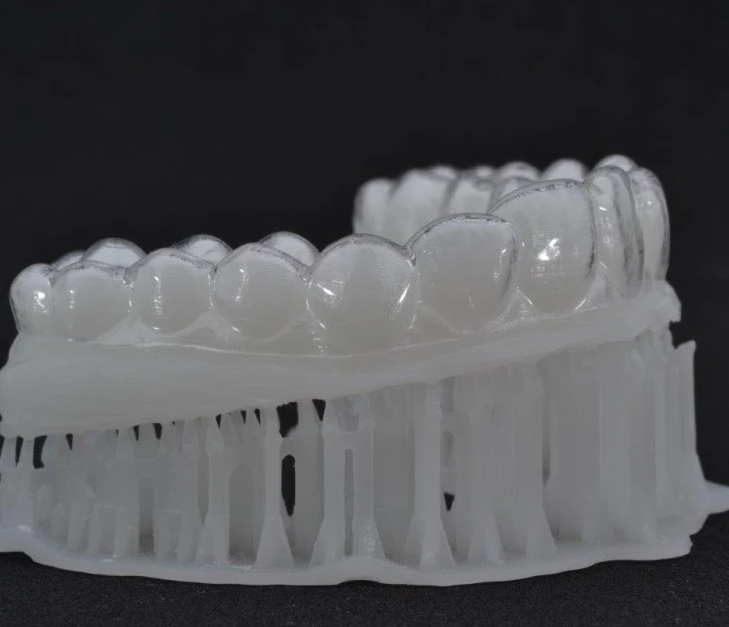
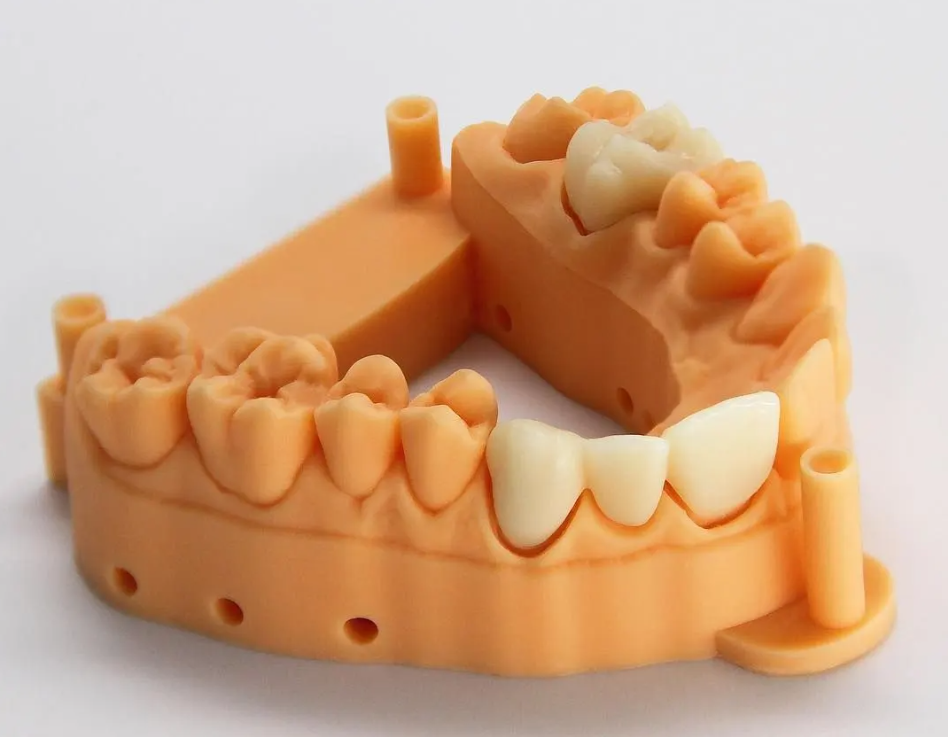
Innovative Applications: Ideal for industries requiring high-quality parts, such as medical devices, jewelry, and automotive components, offering both aesthetic and functional benefits.
Smooth Surface Finish: Resin printing with SLA and DLP technologies produces parts with exceptionally smooth surface finishes, reducing the need for post-processing and making them ideal for applications that require high-quality aesthetics, such as jewelry, dental models, and consumer products.
Contact Us now if you have any questions!
DED: Redefining Metal Manufacturing with Precision and Power
The benefit of DED includes:
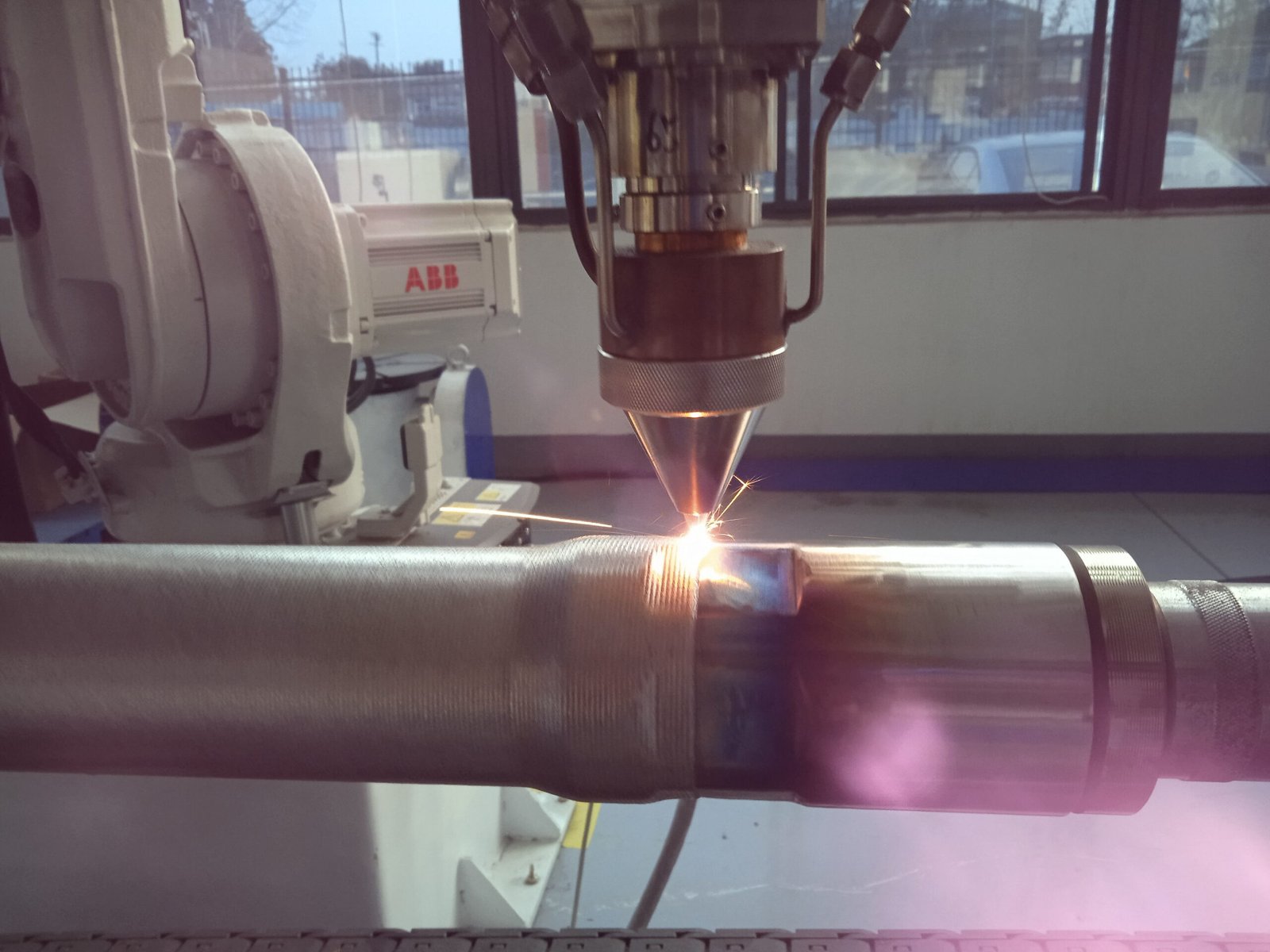
Material Efficiency: DED technology uses only the necessary material to build or repair parts, minimizing waste and reducing material costs, especially in metal manufacturing.
Versatility in Applications: From aerospace and automotive to defense and medical, DED is ideal for both new builds and the repair or enhancement of existing components.
Large-Scale Manufacturing: Capable of producing large, complex parts that would be difficult or impossible with other additive manufacturing technologies.
Rapid Prototyping and Repair: DED allows for quick production and repair of critical components, reducing downtime and accelerating innovation.
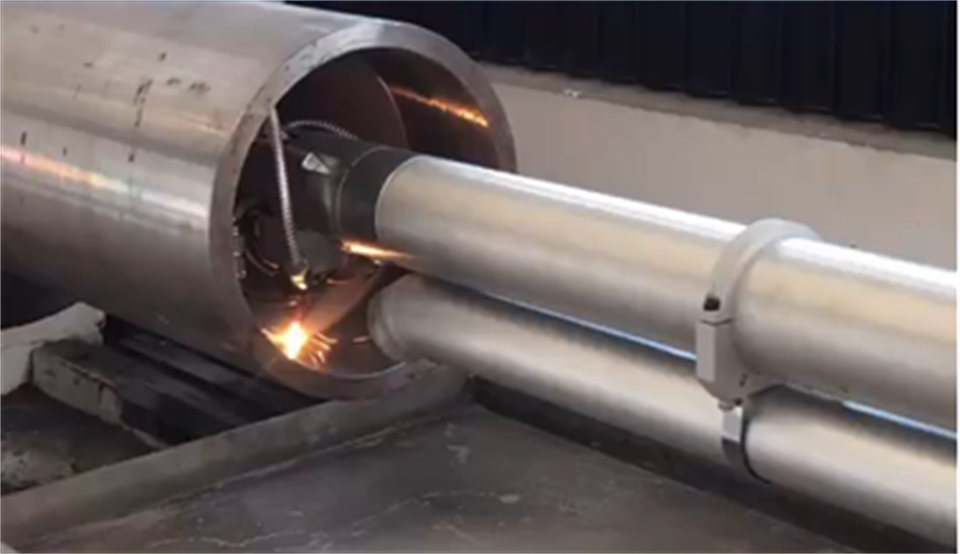
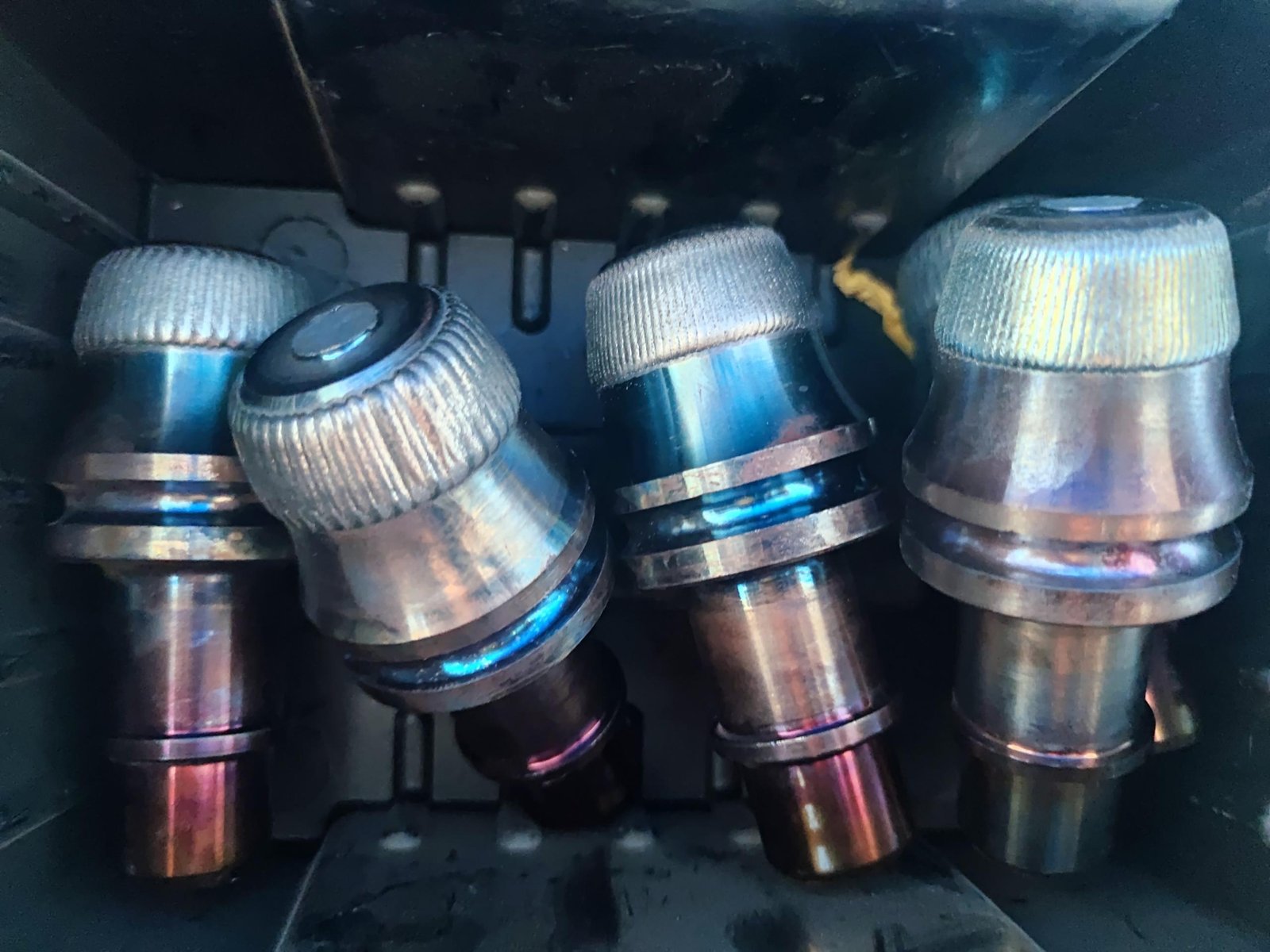
Hybrid Manufacturing: Combine traditional subtractive methods with DED to create hybrid manufacturing processes that enhance productivity and flexibility.
Contact Us now if you have any questions!
Color Printer: Where Precision Meets Vibrant Colors
Binder Jetting VS. MultiJet Printing
Choosing the Right Technology
Binder Jetting
Uses a liquid binding agent to bond powder materials layer by layer.
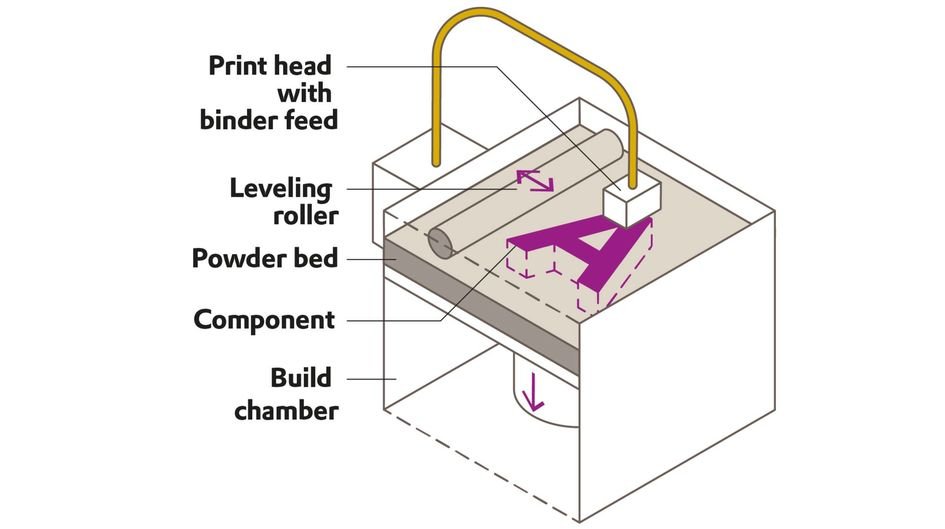
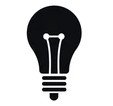
Full-color printing by mixing colored binders with powder materials.
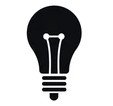
Supports metals, ceramics, and sand powders.
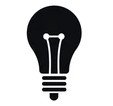
Rougher finish; post-processing may be required.
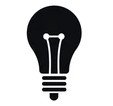
Fast production speed; suitable for large batch production.
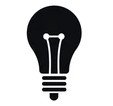
Good for larger parts but lower resolution.
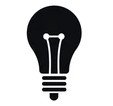
Best for functional parts, prototypes, and casting molds.
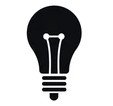
Requires sintering or infiltration for metal parts.
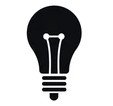
Generally more cost-effective for large parts.
MultiJet Printing
Utilizes multiple nozzles to jet and cure photopolymer droplets layer by layer.
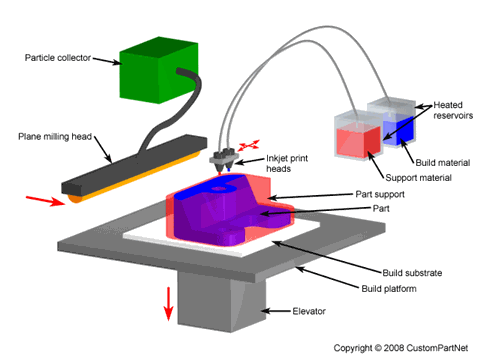
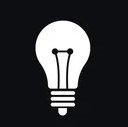
High-resolution color through precise layering of colored photopolymers.
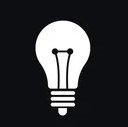
Primarily uses photopolymers, some systems support waxes.
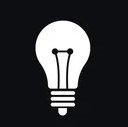
Smooth finish with fine detail, minimal post-processing needed.
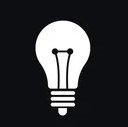
Moderate production speed; provides high detail but may be slower for larger parts.
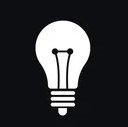
High precision and detail, ideal for intricate designs.
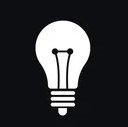
Ideal for detailed prototypes, medical models, and consumer products.
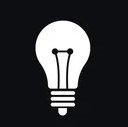
Minimal post-processing, typically UV curing.
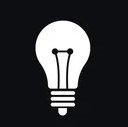
More expensive due to higher resolution and material costs.
The benefit of color printing includes:
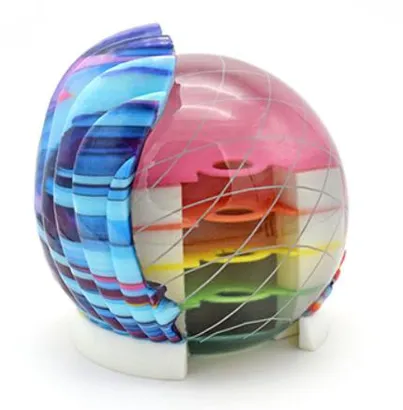
Full-Color Capabilities: Binder Jetting and MultiJet Printing technologies enable the creation of vibrant, multi-color 3D prints in a single process. Ideal for prototyping, architectural models, and consumer products where visual appeal is critical.
High Resolution and Detail: Both technologies offer high precision and fine detail, ensuring that your colorful 3D models are not only visually stunning but also highly accurate and functional.
Wide Material Range: These technologies support a variety of materials, including polymers, ceramics, and composites, allowing for multi-material printing and enhanced versatility in product design.
Efficient Production: MultiJet and Binder Jetting technologies enable faster production times by simultaneously printing multiple parts in full color, making them ideal for batch production and reducing lead times.
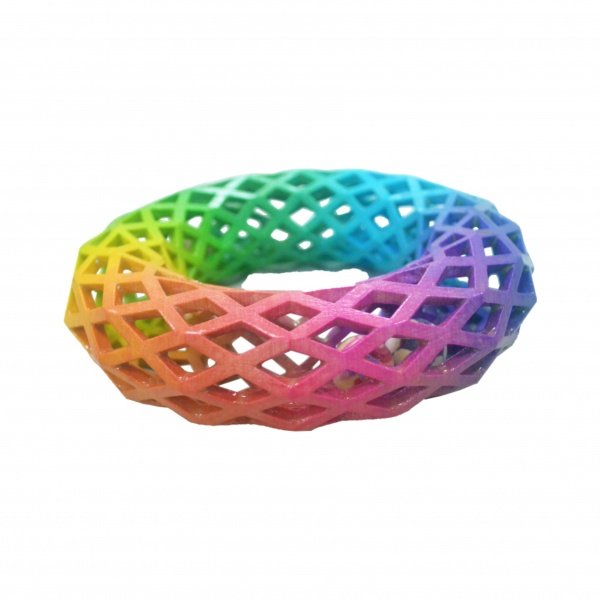
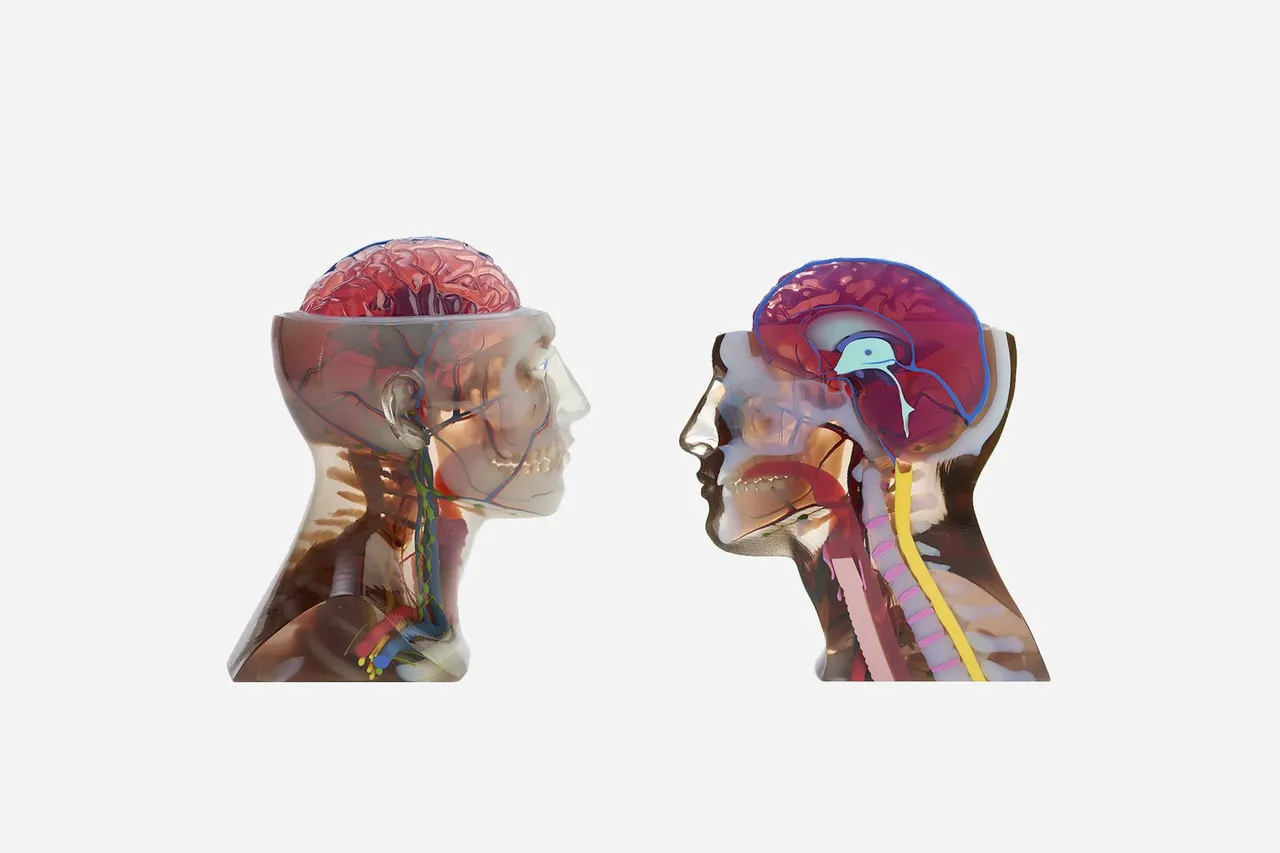
Cost-Effective Prototyping: By combining multi-color and high-resolution printing, these technologies offer cost-effective solutions for producing prototypes and models that closely resemble final products, reducing the need for additional finishing steps.
Contact Us now if you have any questions!
Advanced Ceramic Additive Manufacturing Using Binder Jetting
The benefit of ceramic printing using binder jetting includes:
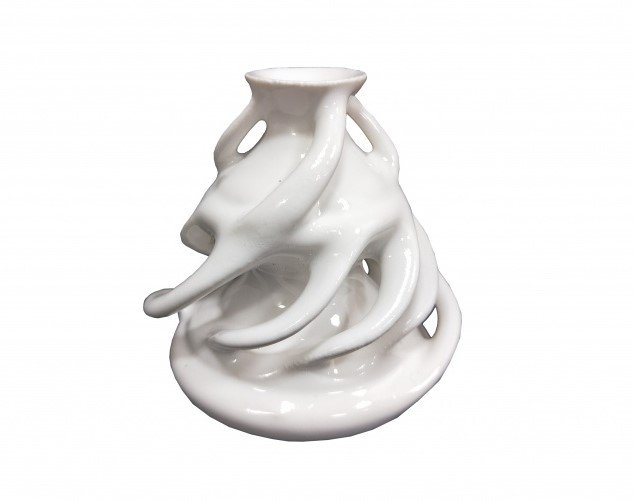
Complex Geometries: This technology enables the production of highly intricate and detailed ceramic components, which are often difficult or impossible to create with traditional ceramic manufacturing methods. It allows for the design of complex internal structures, overhangs, and fine details with precision.
Scalability: Binder Jetting is highly scalable, making it suitable for both rapid prototyping and full-scale production runs. Whether creating one-off custom parts or producing large quantities of components, the process can be adapted to meet varying production needs.
Material Efficiency: Binder Jetting is an additive process, which means it only uses the exact amount of ceramic powder required for each part. This reduces material waste significantly, making the process more cost-effective and environmentally friendly compared to subtractive manufacturing methods.
Customization: The technology supports the creation of customized ceramic parts, allowing manufacturers to tailor products to specific customer requirements. This is especially beneficial in fields such as healthcare, where patient-specific implants and medical devices can be produced.
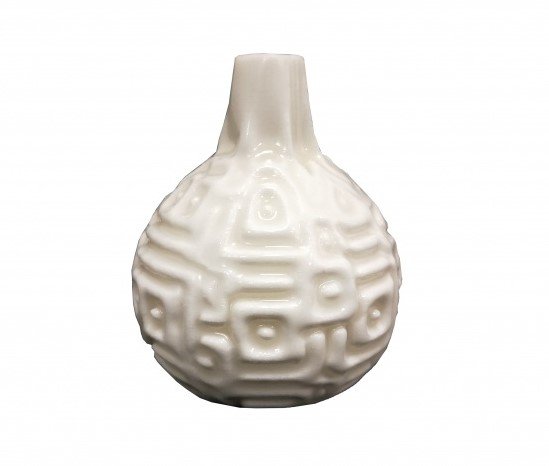
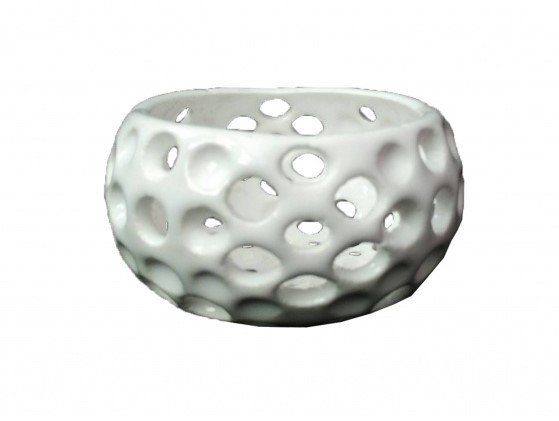
Enhanced Properties: Sintered ceramic parts made with Binder Jetting exhibit excellent thermal resistance, chemical stability, and mechanical strength. These properties make them ideal for applications in demanding industries such as aerospace, electronics, and medical devices, where reliability and performance are critical.
Contact Us now if you have any questions!
Powerful Pellet FDM 3D Printing: Large-Scale, Cost-Effective, and Versatile
The benefit of pellet FDM 3D printing includes:
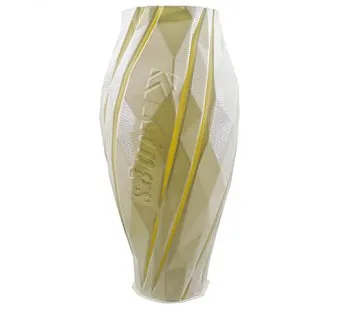
Cost-Efficiency:
Pellet FDM 3D printing significantly reduces material costs compared to filament-based printing. Thermoplastic granules are cheaper to produce and purchase in bulk, making this method more affordable, especially for large-scale production.
Faster Production:
The use of pellets allows for higher extrusion rates, resulting in faster print speeds. This is particularly beneficial for printing large objects, where speed can be a critical factor in meeting production deadlines.
Material Versatility:
Pellet FDM 3D printers can process a wide range of materials, including flexible, rigid, and high-performance thermoplastics. This versatility enables the creation of parts that meet specific mechanical and thermal properties, making it adaptable for various industrial applications.
Scalability for Large Projects:
Pellet FDM is ideal for producing large-scale parts that are difficult or expensive to create with filament-based printers. The ability to extrude larger volumes of material enables the construction of bigger objects with greater efficiency, making it suitable for industries like construction, automotive, and manufacturing.
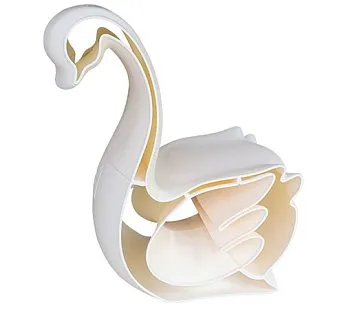
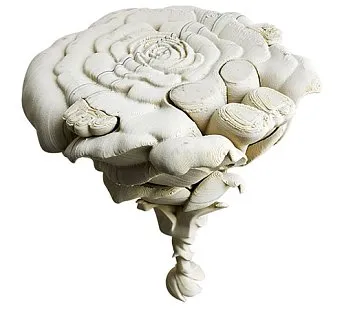
Eco-Friendly and Sustainable:
Pellet FDM technology supports the use of recycled materials, contributing to more sustainable manufacturing practices. By recycling plastic waste into pellets, companies can reduce their environmental impact and promote a circular economy.
High Strength and Durability: The technology is capable of producing parts with high structural integrity and durability, which is essential for applications requiring robust components, such as industrial tools, automotive parts, and construction elements.
Contact Us now if you have any questions!
Elevate Your Production with High-Temperature FDM 3D Printing: Strength, Precision, and Performance
The benefit of high temperature FDM 3D printing includes:
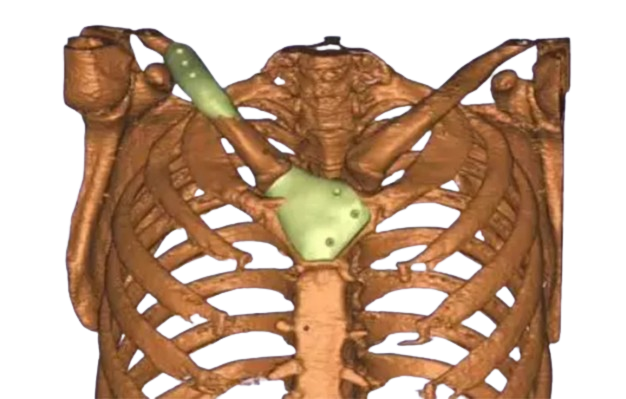
Versatile Material Use:
High-temperature FDM pellet 3D printing supports a wide range of advanced thermoplastic materials such as PEEK, PEI, PPSU, and their composites. These materials provide exceptional mechanical strength, chemical resistance, and thermal stability, making them suitable for demanding applications in industries like aerospace, automotive, and medical.
Cost-Effective Manufacturing:
Utilizing thermoplastic pellets instead of filament significantly reduces material costs. Pellets are generally more affordable and can be purchased in bulk, making high-temperature FDM printing a cost-effective choice for producing large parts or high-volume runs. This cost efficiency is particularly advantageous for industrial-scale production and prototype development.
Enhanced Durability and Performance:
Parts produced with high-temperature FDM technology exhibit superior durability and resistance to high temperatures. The ability to print with high-performance materials ensures that the end products can withstand harsh environments and extreme conditions, which is crucial for applications requiring robust, long-lasting components.
Increased Production Speed:
The high extrusion rates achievable with pellet-based systems allow for faster printing of large objects. This acceleration in production speed not only reduces manufacturing time but also increases overall throughput, making it ideal for projects that demand quick turnaround times without compromising on quality.


Precise Temperature Control:
Advanced temperature management features, including high-temperature extruders, heated build chambers, and precise PID auto-tuning, ensure optimal printing conditions. This control minimizes warping and deformation, enhances the accuracy of dimensional measurements, and ensures consistent quality across different prints.
Large Build Volume Capabilities:
High-temperature FDM printers can accommodate larger build volumes, enabling the production of sizable parts in a single print job. This capability is particularly valuable for creating large industrial components, custom tooling, and intricate prototypes that would otherwise require assembly from smaller printed sections.
Contact Us now if you have any questions!
Experience Large-Scale Innovation with the Mobility of Robotic Arm FDM Printing
The benefit of robotic arm FDM 3D printing includes:
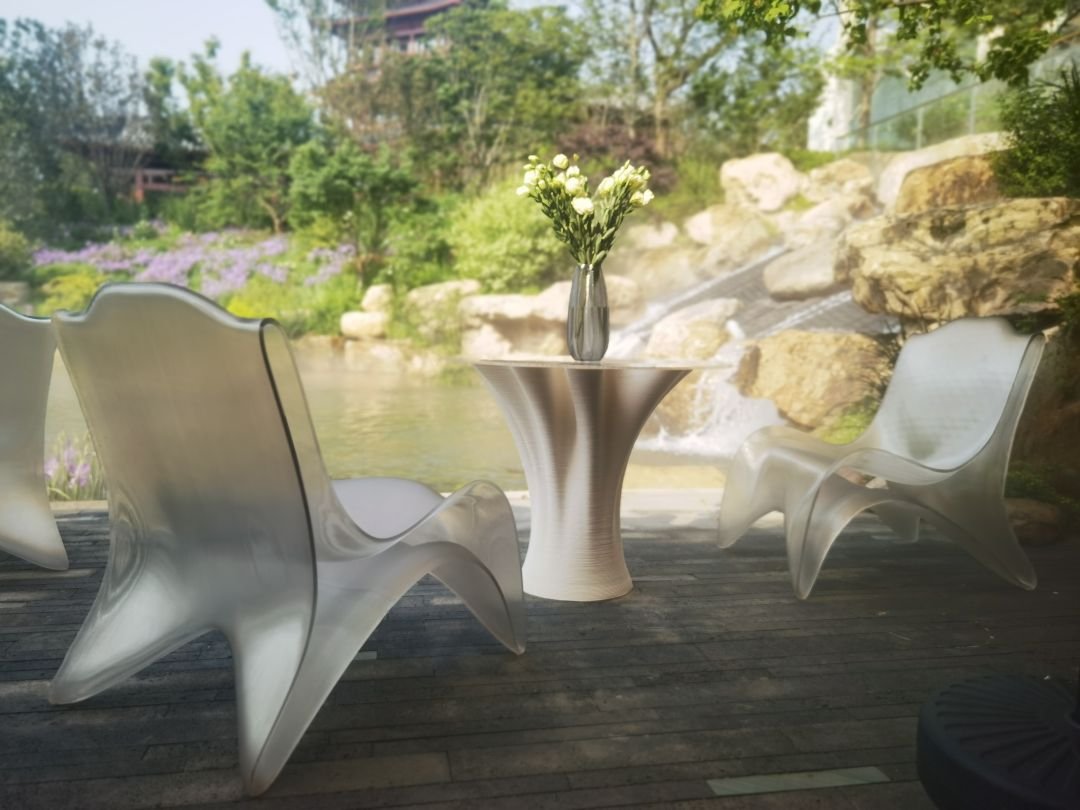
Complex Geometries:
The robotic arm’s flexibility allows for intricate and detailed designs that traditional FDM printers struggle to achieve. It can print on multiple angles and orientations, accommodating complex shapes and structures.
Large Build Volume:
With its extended reach, the robotic arm can handle larger print volumes, enabling the production of bigger components and prototypes in a single print session, which reduces the need for assembly.
Material Variety:
The system supports a wide range of thermoplastic materials, including advanced composites and high-performance filaments, making it suitable for diverse applications from industrial parts to custom prototypes.
Efficient Production:
The ability to print large and complex parts in one go streamlines the production process, minimizes material waste, and reduces post-processing and assembly time, enhancing overall efficiency.


High Precision and Detail:
Advanced control systems ensure accurate material deposition and fine detail, resulting in high-quality prints with precise dimensions and surface finish.
Contact Us now if you have any questions!
Transforming Big Ideas into Reality: High-Speed, Large-Volume FDM 3D Printing for Custom Solutions
The benefit of large scale FDM 3D printing includes:
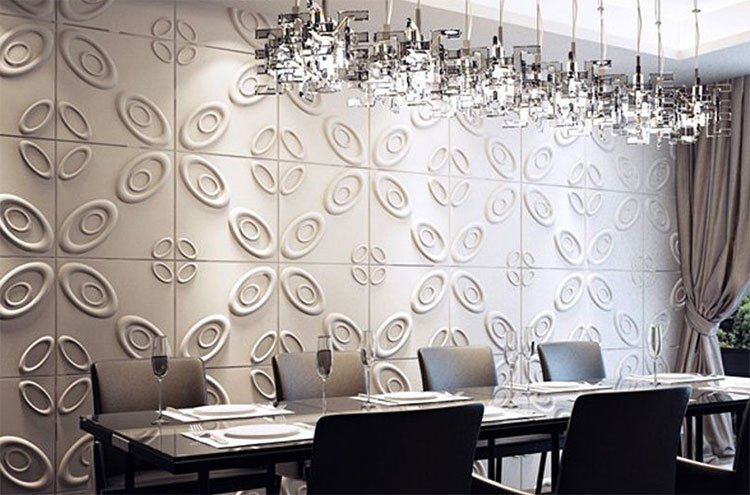
Cost Savings:
Large-scale FDM 3D printing significantly reduces material costs by using bulk thermoplastics and eliminating the need for expensive molds and tooling. This approach not only cuts production expenses but also minimizes waste by using only the necessary amount of material.
Customizable Production:
The technology allows for the creation of custom, large-scale parts with ease. Unlike traditional manufacturing methods, which require extensive retooling for changes, large-scale FDM printing can quickly adapt to new designs without the need for expensive modifications to production lines.
Scalability:
FDM 3D printing technology is highly scalable, making it suitable for producing both small prototypes and large, functional components. This flexibility accommodates a wide range of industrial needs, from detailed prototypes to full-sized parts for various applications.
Faster Turnaround:
The high-speed printing capabilities of large-scale FDM technology accelerate the manufacturing process. By shortening the time from design to final product, businesses can rapidly iterate on designs, reduce lead times, and meet tight deadlines more effectively.

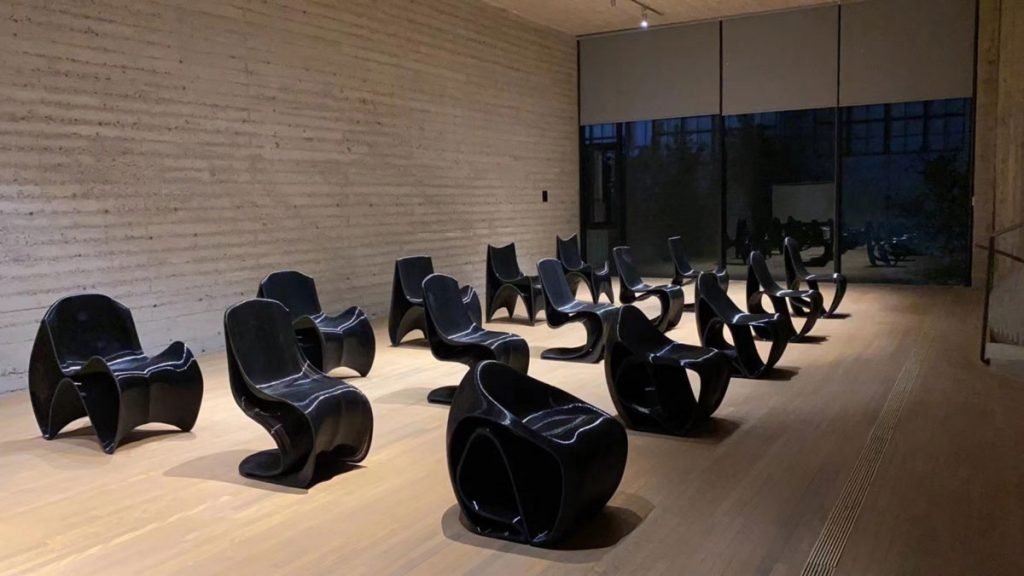
Material Variety:
Large-scale FDM printers support a broad range of materials, including specialized thermoplastics and composites. This versatility makes them ideal for producing parts with specific properties required for applications in industries such as aerospace, automotive, and construction.
Contact Us now if you have any questions!
Precision Sand Molds Made Simple: Discover the Future of Casting with Our 3D Printer
The benefit of sand casting 3D printing includes:

Cost Reduction:
Sand casting 3D printing minimizes material waste by precisely depositing sand and binder where needed, significantly reducing the cost associated with excess material and mold rework. Additionally, it eliminates the need for expensive traditional tooling, which further reduces upfront costs for custom or low-volume production.
Complex Geometries:
Sand casting 3D printing dramatically speeds up the production of molds by eliminating the need for creating physical patterns and molds through conventional methods. This not only accelerates the production process but also shortens the product development cycle, enabling faster time-to-market. The flexibility of 3D printing means molds can be modified or customized easily without delays.
Enhanced Quality and Consistency:
The precision of 3D printing technology ensures consistent quality in every mold produced. Digital control over the entire process reduces human error and variability, resulting in higher-quality casts with improved accuracy and dimensional stability. This is particularly valuable in industries where part consistency and reliability are critical.
Environmental Impact:
By reducing material waste and enabling the use of eco-friendly binders, sand casting 3D printing technology offers a more sustainable manufacturing solution. It contributes to lowering the carbon footprint by optimizing material usage and eliminating the need for traditional tooling and patterns, which are often discarded after use.
Wide Range of Applications:
Sand casting 3D printing is applicable across a diverse range of industries, including automotive, aerospace, energy, and industrial manufacturing. Its versatility allows it to be used for everything from large-scale production parts to specialized custom components, broadening the scope of its applications and increasing its value in various markets.
Contact Us now if you have any questions!